22/2/2017
Activity:
-Study more about dialyser and peristaltic pump
- study more about the hemodialysis
Objective:
- To more understand about the haemodialysis before develop the prototype.
- To more understand about the main part of the project which is dialyser and peristaltic pump.
Content/procedure:
The bipolar stepper motor usually has four wires coming out of it. Unlike unipolar steppers, bipolar steppers have no common center connection. They have two independent sets of coils instead. You can distinguish them from unipolar steppers by measuring the resistance between the wires. You should find two pairs of wires with equal resistance. If you've got the leads of your meter connected to two wires that are not connected (i.e. not attached to the same coil), you should see infinite resistance (or no continuity).
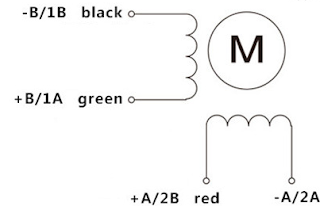 |
Figure 1: The stepper motor coils |
There are two types of dialysis: hemodialysis and peritoneal
dialysis. In hemodialysis, blood is passed through an artificial kidney
(hemodialyzer) to clean it. Peritoneal dialysis uses a filtering process like
hemodialysis, but the blood is cleaned inside the body rather than in a machine.
Peritoneal dialysis is a treatment for kidney failure that
uses the lining of your abdomen, or belly, to filter the blood inside a body.
Doctors call this lining the peritoneum. A doctor will place a catheter in a
belly a few weeks before start the treatment.
When the peritoneal dialysis is start, dialysis solution
like a water with salt and other additives will flows from a bag through the
catheter into a belly. When the bag is empty, the catheter can disconnect from
the bag and cap it so patient can move around and do normal activities. While
the dialysis solution is inside a belly, it soaks up wastes and extra fluid
from the body. After a few hours, drain the used dialysis solution into a drain
bag. Patient can then dispose of the used dialysis solution, which is now full
of wastes and extra fluid, in a toilet or down the drain of a sink or bathtub.
Then start over with a fresh bag of dialysis solution.
In hemodialysis, blood is removed from the body and
circulated through an extracorporeal fluid circuit (outside the body), then
returned to the patient. This circuit includes a hemodialyzer, which is where
the blood is cleaned. The hemodialyzer contains a selectively permeable
membrane, which is a filter that allows fluids and waste (uremic toxins) to
pass through, but prevents the exchange of blood components, microorganisms and
the "skeletons" of dead microorganisms (endotoxins). The fluid used
to clean the blood (dialysate) flows in the opposite direction to the blood on
the opposite side of the membrane, while waste and extra fluid are removed from
the blood and end up in the dialysate
Result and analysis
I has choose the hemodialysis treatment because it is most often
done by trained health professionals who can watch for any problems. It allows
patient to be in contact with other people having dialysis, which may give
emotional support to patients. Also, patient don't have to do it by their self,
as do with peritoneal dialysis. While the peritoneal can increases the risk for an infection of the
lining of the belly, called peritonitis. For the peristaltic pump, I will use stepper motor bipolar series. Bipolar motor have high torque.
Conclusion
Proceed to buying the component next week to start the design the circuit and simulating the circuit using Proteus. Also, to study about the dialyser controlling process.